Scan part while the laser immediately indicates the correct position in the control cabinet. Without expert knowledge, the assembly process becomes accessible to everyone.
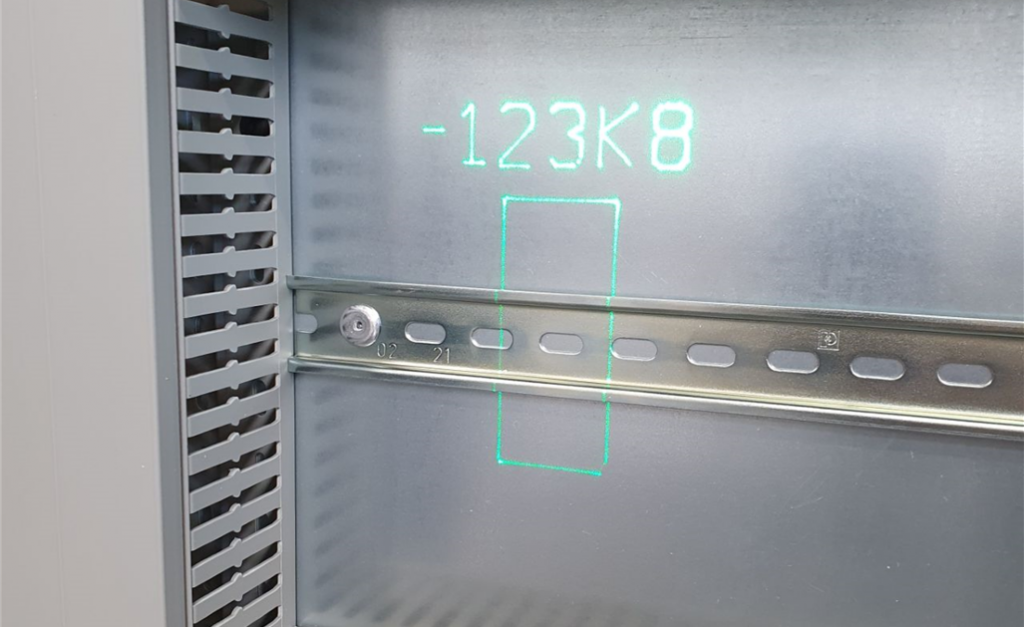
Background:
PIA Service has all the disciplines and knowledge required for industrial automation. As a system integrator, they offer you full support for process and machine controls. In this company with 45 employees, control panels are designed, manufactured and assembled.
case:
Like so many technical companies, Pia Service is constantly faced with competition from low-wage countries and is therefore always working on cost price reduction through production optimisation. One of the stated goals is to carry out the assembly process completely paperless.
In addition, the panel construction and electrical industry has great difficulty retaining and attracting sufficient staff, which means that the scope for new employees must be broadened to other target groups. It concerns technically high-quality work, but no specific prior knowledge is required for the assembly. This offered opportunities to properly instruct less technically trained personnel by means of visualization.
Solution:
Together with the Virtutec project team, we translated the assembly instructions to ProCon. The software was then made available on special kiosks equipped with touchscreens with laser projection, supplemented with a wireless barcode scanner.
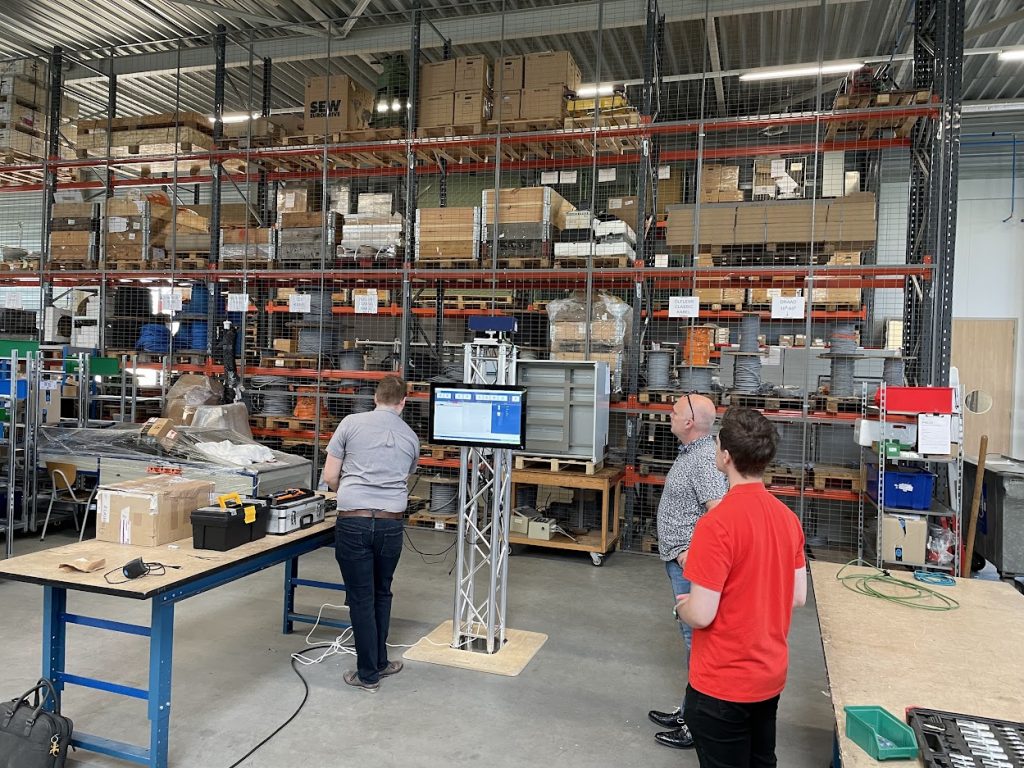
The column can be placed at a fixed location as desired, or in this case it can be set up flexibly.
The operation has been simplified in such a way that the technician uses the barcode scanner to scan a new product from the storage bin. After that the touchscreen and the laser immediately illuminate the correct mounting location (including ODC code) in the switch box on the mounting wall. The software indicates per part which article must be attached in which location and equal parts are shown successively. The technician performs, can set the pace and deliver quality… without a long training period.
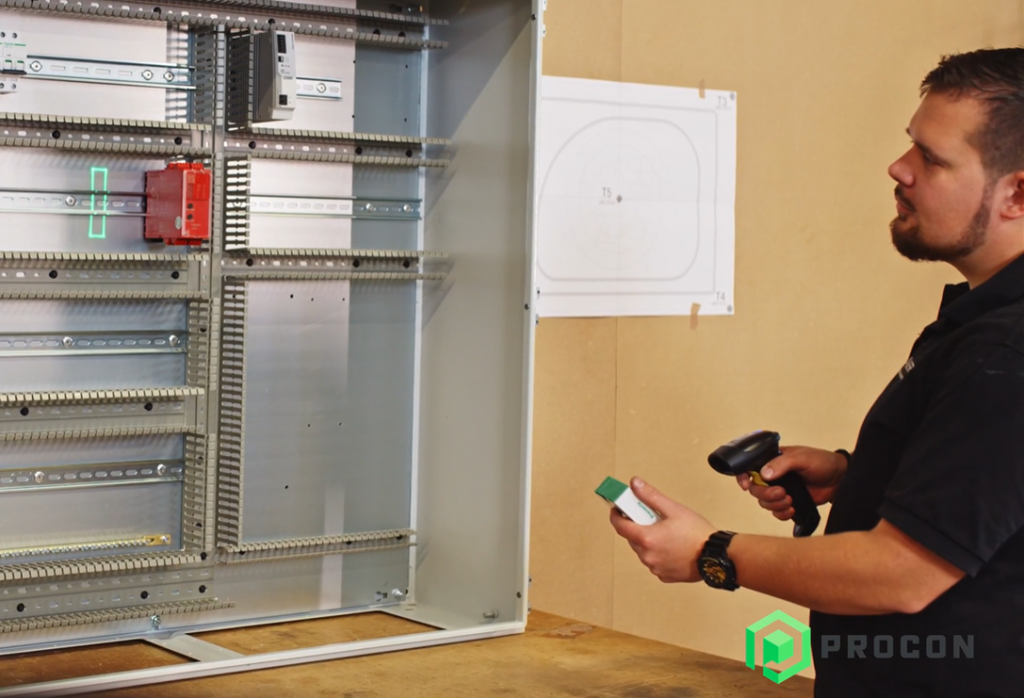
In this way, the detection of often long and difficult article codes is ‘taken over’ by the system, minimizing the chance of errors due to overwriting or miscommunication, for example, and ensuring that the ‘first time right’ principle works correctly.
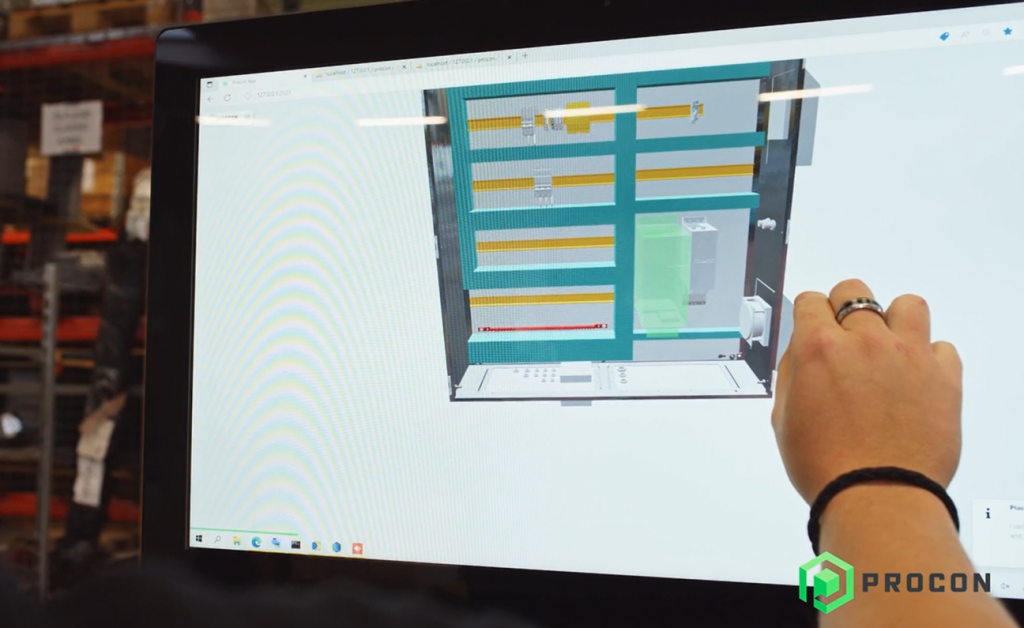
After scanning, the part is shown in green on the screen so that the positioning becomes even clearer for the operator.
The backend system keeps track of whether all parts of the bill of materials (BOM) have been used and whether additional parts are installed. In the overview for the work planner or assembly manager it is easy to see how far the assembly has progressed and to what extent there is still waiting for parts to be ‘received’. In the case of ‘too many parts’ (additional with regard to BOM), this is reported and the operator cannot place the part ‘for approval’.
Optionally, you can also choose to work without a scanner, in which case the assembly sequence is determined by the structure of the 3D model. This can also be adjusted as desired, so that assembly processes can actually be carried out without hindrance and in the most ideal way. This is how the system works for you!
websites:
DEMONSTRATION FILM:
Would you also like to work on process optimization and cost reduction?
Or read more about us or our references first